In any industrial plant, pressure gauges aren’t just tools, they are safeguards. They protect equipment, keep processes on track, and in many cases, prevent costly or dangerous failures. And when accuracy, visibility, and durability are non-negotiable, a digital pressure gauge can outperform its analog counterpart every time.
At Automation Products Group, Inc. (APG), we provide digital pressure gauges for everything from medical devices to aircraft maintenance to sugar mills. Over the years, we’ve identified three situations where a digital gauge isn’t just a better choice, it’s the right choice:
- When precision matters for calibration & testing
- When visibility & control can make or break a process
- When your equipment must survive harsh, punishing environments
Calibration & Testing
Accuracy is never more important than during calibration and testing. While a typical analog gauge might offer an error band of ±1%, many digital pressure gauges deliver accuracy within ±0.1%—ten times better. If you’re testing, calibrating, or monitoring vital equipment, a digital pressure gauge ensures you know the exact pressure at any moment.
Case in Point: Infusion Pump Alarm Calibration
Infusion pumps deliver fluids into a patient’s circulatory system through an IV. Each pump’s Downstream Occlusion Alarm detects pressure build up on the discharge side of the pump and alerts medical staff that the line is obstructed.
Its reliable operation is absolutely critical for patient’s safety and the liability of the healthcare institution. Hospitals rely on APG’s PG5 digital pressure gauge for this task. With a range of 30.0 psig and accuracy of ±0.03 psig ( 0.1% of full scale), it keeps alarms within spec and ensures life-saving equipment works exactly as intended.
Case in Point: Locomotive Brake Leak Detection
Detecting a brake leak means detecting minute changes in pressure on a full scale. One locomotive manufacturer uses APG’s PG5 digital pressure gauges to monitor their brake lines. They’re looking for pressure changes as low as 0.023 PSI on a 20.00 PSI gauge. With resolution down to 0.001 PSI, the PG5 makes pinpoint leak detection possible.
Improve Visibility & Control
Digital pressure gauges do more than display data, they also enhance process control. Large, easy-to-read displays, built-in conversions, and integration with control systems give operators the information they need, exactly when they need it.
Case in Point: Aircraft Lifts
Air Force maintenance crews work on aging B-52 bombers. When the aircraft is down for maintenance, the crew uses 38 jacks with APG’s PG10 digital pressure gauges installed to lift the aircraft off the floor. Using a digital pressure gauge allows the maintenance crew to carefully lift the aircraft evenly, preventing structural stress and extending the life of the aircraft.
Case in Point: Pump Control
A sugar mill in Central America invested in APG’s PG7 digital pressure gauges for pump monitoring and control with great success. The digital format makes reading the gauges much easier when vibration picks up—a common occurrence in any processing plant. The gauges not only helped with clear readings, but also:
- Send data to SCADA system
- Triggered alarms and shut down pumps
- Convert PSI to head for pump curve comparisons.
For especially harsh installations, APG offers remote displays connected by cable. This removes and protects the electronics from the vibration, heat, or mess of the connection point to the process, and extends the life of the sensor.
Durability In Harsh Environments
In tough conditions, analog gauges can fail quickly. Bourdon tubes can clog, and moving parts can wear out. Digital gauges, with no moving parts and better resistance to overpressure, are intrinsically more durable.
Case in Point: Filter Monitoring in Pulp and Paper
A paper towel manufacturing plant filters pulp from waste ink used in the printing process. In this messy environment, a bourdon tube on an analog gauge would quickly foul with so much paper pulp in the ink, where the digital pressure gauge is unaffected—no diaphragm seal required and no bourdon tube to foul up. The digital pressure gauge also sends a signal to the HMI (Human-Machine Interface) control system to notify personnel when the filter needs changing.
When Your Gauge Should Be Digital
The bottom line: choose a digital pressure gauge whenever you need extreme accuracy, clearer readings, greater control, or unmatched durability out of your pressure gauge. Doing so will improve the overall safety and reliability across your operation.
At APG, we don’t just sell gauges, we help you choose and customize the right one for your exact application. Whether you’re working in a clean lab, a busy plant floor, or the harshest outdoor environment, we’ll build a digital pressure gauge the works as hard as you do.
Let’s talk about your application and design the gauge that keeps your operation at its best.
WRITTEN BY
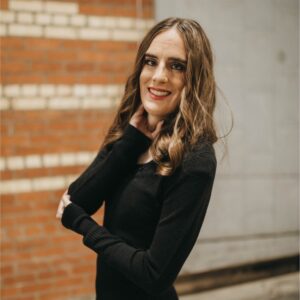
Sami T.
Sami Thompson is APG’s Marketing Technical Writer and has been with the company since 2022. With a master’s degree in English from Utah State University and a 40-page thesis publication under her belt, Sami has a demonstrated strong writing background. In her free time, Sami enjoys reading and birdwatching.