Pressure transducers are highly popular measurement devices, built to fit in many different environments and chemicals. At Automation Products Group, Inc. (APG), we offer a variety of pressure transducers. In this post, we’ll cover the basics of pressure transducers, including how they work and the applications they excel in.
What Is a Pressure Transducer?
A pressure transducer is a sensor used to measure pressure and then convert that pressure reading into a continuous signal output. It can provide critical data about the pressure in a pipe or tank, the weight of an object, or even the depth of fluid above it. Most industrial pressure transducers are made of three parts: a transducer and a transmitter, which are inside the housing.
What Is a Transducer?
A transducer converts a physical action, often a vibration, into an electrical signal. Examples include microphones and electrical guitar pickups. Pressure transducers convert pressure, such as air pressure, fluid pressure, and oil pressure, into electrical signals.
Types of Pressure Transducers
-
- Piezoelectric Pressure Transducers
Piezoelectric pressure transducers are devices that use the piezoelectric effect to measure any changes in acceleration, pressure, strain, temperature, or force. These transducers produce a voltage when they flex, converting the measured energy into an electric charge.
- Piezoelectric Pressure Transducers
-
- Piezoresistive Pressure Transducer
This pressure transducer uses the change in electrical resistance of a material when that material is being stretched. Unlike piezoelectric transducers, which generate voltage, piezoresistive transducers modify circuit resistance to convey measurements.
- Piezoresistive Pressure Transducer
How A Pressure Transducer Works
A pressure transducer operates through an electrical circuit that’s connected to a diaphragm. As the diaphragm is exposed to changes, the diaphragm flexes, changing the characteristics of the circuit. The transmitter then converts the measurement into a standardized signal, such as 4-20 mA or Modbus, and communicates it to whatever control or display system it’s connected to.
Pressure Transducer Type Reference
There are five main types of pressure measurement:
-
- Gauge Pressure: Measures pressure relative to atmospheric pressure, with a vented body to adapt to atmospheric changes.
- Vacuum Pressure: Registers negative pressure relative to atmospheric pressure, also vented.
- Compound Pressure: Combines gauge and vacuum measurements, vented for atmospheric changes.
- Sealed Pressure: Body sealed to protect from environmental hazards, suitable for high-pressure measurements unaffected by atmospheric changes.
- Absolute Pressure: Sealed under vacuum, used for low-pressure ranges to observe atmospheric changes.
Choosing A Pressure Transducer
Selecting the right transducer involves considering:
-
- What pressure range will the transducer measure under “normal” circumstances?
- What pressures might the transducer face under “abnormal” circumstances?
- How will the transducer be connected to the pipe, tank, line, vessel in which it is measuring pressure?
- Will the transducer be measuring a substance that is corrosive or chemically aggressive?
- Will the transducer body be exposed to the elements, somewhat sheltered, or submersed in liquid?
- Will the transducer be exposed to strong vibrations, shocks, or otherwise rough treatment?
Pressure Transducer Applications
Pressure transducers are versatile and can be used in:
-
- Monitoring line pressure in commercial or industrial systems.
- Measuring weight applied by hydraulic rams.
- Calculation liquid levels in vessels.
- Ensuring appropriate pressure in pressurized systems.
They are essential in environments like fracking rigs, industrial processes, water systems, and more.
Best Practices for Pressure Transducers
Follow these tips for optimal performance:
-
- Do not touch the diaphragm on any transducer.
- Only install a transducer in an environment it is designed to operate in.
- For threaded process connections, use PTFE tape as necessary, and appropriately.
-
-
- Be sure to match straight threaded sensors with straight threaded process connections and tapered threaded sensors with tapered-thread connections.
-
-
- Do not over tighten process connections.
- Ensure desiccant cartridges for submersible pressure transducers are situated in a dry location that is easily accessed and observable.
- Check sensor networks for ground loops.
- Check units at least yearly for recalibration.
If you have further questions about pressure transducers, including how they can help your system operate safely, let us know. Our Measurement Experts can help you find the right technology to fit your application. Give us a call or drop an email today.
WRITTEN BY
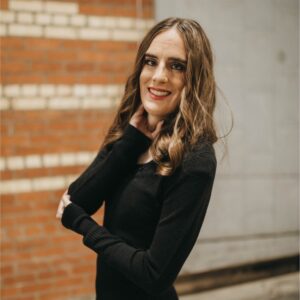
Sami T.
Sami Thompson is APG’s Marketing Technical Writer and has been with the company since 2022. With a master’s degree in English from Utah State University and a 40-page thesis publication under her belt, Sami has a demonstrated strong writing background. In her free time, Sami enjoys reading and birdwatching.