What is a Float Switch?
A float switch is a type of contact liquid level sensor that uses a float to operate a switch. Float switches are commonly used to control other devices, such as alarms and pumps, when a liquid level rises or falls to a specific point. In electrical float switches, floats are used to open and close (i.e., turn off and on) electrical circuits.
Float switches are also often sought after because they are cost-effective, reliable, and can be used with a wide variety of liquids. In this article, we will dive into common uses of float switches, both normally open float switches and normally closed float switches.
Types of Float Switches
There are two types of float switches: stem-mounted float switches and cable-suspended float switches.
Stem-mounted Float Switches
Stem-mounted float switches constrain the movement of the float to up-and-down along a stem. They operate on a one-float-one-level basis. Stem-mounted float switches can be simple or complex—ranging from a single-point switch with a single float on one stem to multi-point switches with up to seven floats on a single stem. Single-point float switches can be found in both vertical and horizontal orientations.
Cable-suspended Float Switches
Cable-suspended float switches, on the other hand, are as free as the cables they are attached to. An untethered cable-suspended float switch will flow as far as the cable allows. While cable-suspended float switches are all mechanically pretty equivalent (float and cable), they can be much more electrically diverse than stem-mounted float switches. Cable float switches can be simple, with a single point that controls a switch, or more complex, with up to four switch points and built-in hysteresis.
How Do Float Switches Work?
Almost all electrical float switches work by using a magnet to open and close a reed switch.
How Stem-mounted Float Switches Work
Stem-mounted float switches use a magnet in a float that passes over the reed switch with the rising or falling action of the liquid, either opening or closing the switch. On horizontal stem-mounted float switches, the float rotates away from the reed switch on a hinged arm, rather than free-floating on a central stem.
How Cable-suspended Float Switches Work
Cable-suspended float switches have both the magnet and the reed switch located in the float. As the float rises and falls with the liquid level, the magnet moves closer to or further away from the reed switch, causing it to open or close. In both cases, the changing liquid level is translated to an electrical on-off signal by the movement of the magnet.
Normally Open Float Switches vs. Normally Closed Float Switches
When purchasing a float switch, most of them have normally open or normally closed operation. There are some single-point, stem-mounted float switches that are user reversible. “Normally” refers to the lowest position of the float where the float is not floating. “Open” means an open circuit, which is off. “Closed” switch completes a circuit, turning it on. Consider if rising or falling liquid levels trigger an action, and whether that action turns a circuit on or off. A normally open switch doesn’t allow any electricity through it when the float is freely hanging. As the water flows into a tank and raises the float, its contacts will close and turns on an emptying pump.
Normally open switches turn on with rising liquid levels and off with falling levels. This makes them great for High Level alarms and controlling emptying pumps, such as sump pumps and sewage lift station pumps. Normally open float switches are used for dewatering, sump and sewage points.
Conversely, a normally closed switch will turn off with rising liquid levels and on with falling levels. They are often used for Low Level alarms and filling pumps. As an example, a float switch triggering an low-level alarm would call for a normally closed float switch. Likewise, turning off an emptying pump when the level in a tank gets too low calls for a normally open switch.
Float Switch Setup and Installation Best Practices
We’ve put together a few tips on best practices for setting up and installing float switches.
Begin by ensuring that the float switch is compatible with the liquid it will be placed in. Next, take care to mount each float switch correctly.
For stem-mounted float switches, ensure the mount is liquid tight. Whether mounted outside or inside the vessel, the stems aren’t made for submersion and a leak around the mount can affect the performance.
If the float switch is cable-suspended, verifying your physical setup is important. Check the following for the best results:
-
- Is the junction box the float switch will connect to above the high-water mark?
- When connected to that junction box, will the float switch reach the desired lowest switch point?
- Does the float switch need to be tethered to keep it from floating out of position or into the path of inlet/outlet pipes, agitators, etc.?
- Is the float switch’s weight adequately supported, so that it doesn’t pull out of the terminals in the junction box?
Finally, check that the float switch integrates correctly with the control system. For a single switch, hook up two wires. Each additional switch or switch point only adds one wire. Make sure the number of terminals is appropriate for the number of wires coming from the switch(es). The switches can connect to the control system or control circuitry. They can also be directly in-line with the controlled load. If the switches are directly in-line, ensure that there’s adequate protection for them from current and voltage spikes.
Applications for Float Switches
Float switches are used for point-level detection by indicating that a fluid level is at-or-above (normally open), or at-or-below (normally closed) a specific level. Float switches are a great solution for triggering alarms and turning a pump on or off based on a specific level. Float switches can help with knowing when a home heating oil tank is down or automatically turning on a sump pump when the water level reaches a certain point.
With their variety of materials, arrangements, and capabilities, float switches can be found for almost every situation. Small spaces call for small, stem-mounted switches, while cable-suspended float switches are ideal for spaces with wider hysteresis bands. Aggressive chemicals require float switches made of stronger, more resistive materials (like plastics, instead of stainless steel). Explosive atmospheres or high-pressure, high-temperature processes need switches with appropriate certifications.
Float switches are also helpful for reducing complicated automation. For some process systems, a central PLC that monitors and runs everything is necessary for smooth, cost-effective operation. In these situations, a float switch is merely one more data point in a complex scheme. But for smaller applications—say a pump or two on tanks—float switches can be the key to on-going success. Hooking float switches up to the pump-controlling relays might be all the automation necessary. They can empty or fill tanks when required, or alert that pumps did (or didn’t) turn on appropriately. Float switches are great for knowing when specific high or low levels are reached or exceeded.
In the end, the type, material, and operation of the float switch comes down to what best matches the application. Whether complicated or straight forward, small vessels or large reservoirs, common liquids or really aggressive chemicals, there’s a float switch that can fit the job.
Ready to discover how to integrate float switches into your control system? Contact us and our Measurements Experts can match you up with a float switch that will make liquid level measurement one less thing to worry about.
WRITTEN BY
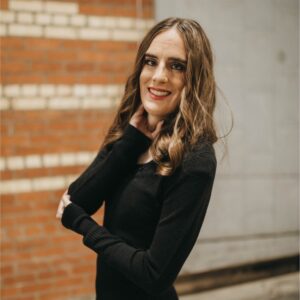
Sami T.
Sami Thompson is APG’s Marketing Technical Writer and has been with the company since 2022. With a master’s degree in English from Utah State University and a 40-page thesis publication under her belt, Sami has a demonstrated strong writing background. In her free time, Sami enjoys reading and birdwatching.