As you may already know, agriculture relies on two things: speed and efficiency. No matter how hard you work, it seems like there’s always more to do, and delays can quickly add up—and that can cost you money.
To meet the demands of the modern farm, you need to be able to get the most out of your equipment, which means you’ll often push your equipment hard, day in and day out.
Whether you’re threshing, fertilizing, or baling, you need your machinery to work as efficiently as possible, running at the highest speed and power imaginable.
Of course, this puts a lot of stress on your equipment, which can, in turn, put you at risk of breakdowns that will cost you time or lead to wasted crops. However, modern farm machinery has many sensors built into them to help monitor your equipment’s condition to prevent breakdowns. These sensors provide you with instant feedback so that you can avoid costly damage.
One of the most valuable—and overlooked—sensors on your agricultural equipment is the torque sensor. This device measures the amount of force occurring to make something turn or spin.
These sensors prevent overdriving your equipment by constantly monitoring torque, saving you from expensive repairs and unnecessary delays. But, first, let’s take a deeper look at how torque sensors work.
What is Torque?
Before we start looking at torque sensors, it’s helpful to take a moment and talk about what precisely “torque” means. Torque has to do with forces that twist an object, but it’s worth knowing how torque relates to other forces present in your machinery.
At a basic level, torque is a force that propels an object to spin or rotate around a central axis. Take a nut threaded onto a bolt, for example. The force that moves the nut up and down the bolt is torque, and the more torque you apply to a nut, the tighter the connection will be once that nut is driven home.
In terms of your equipment, though, it helps think of torque with two other values: revolutions per minute (RPM) and horsepower. The first is pretty straightforward: RPM is simply the number of times a motor’s shaft rotates every minute. The higher the RPM, the faster the engine is running.
Horsepower, on the other hand, describes the amount of power an engine produces. When you’re calculating horsepower, you multiply the amount of force your engine is making by the distance that force propels an object, then divide that number by the time it takes to perform the work. One unit of horsepower is equal to 550 foot-pounds per second.
If you’re looking to improve the power output of your equipment, you should avoid trying to increase the RPM. Instead of raising power output, you’ll decrease your engine’s torque while consuming more energy. Instead, increasing torque is the best way to expand your equipment’s horsepower.
For many of your applications, it’s torque that’s doing the work. Efficient torque usage helps spread fertilizer evenly, break up difficult soil, and move through your fields without getting bogged down.
Torque is the driving force behind most of your equipment, and that makes torque measurement incredibly important.
Torque Measurements
The question, then, becomes how to measure torque. That’s where an accurate, reliable torque sensor comes into play.
Torque sensors provide instant feedback for equipment operators, allowing them to monitor power output and machine strain to adjust machinery for optimal efficiency.
A torque sensor is a kind of transducer, which measures torque forces and changes them into an electrical signal that an electric receiver can interpret. A torque transducer allows you to constantly monitor torque as your equipment operates since the electrical signal transmitted from your sensor increases in proportion to the amount of torque detected.
All torque sensors use the same basic principle: the strain gauge. For example, a torsion sensor involves a metal body bonded to a neutral polyimide film, with strain gauges made of foil attached. As these strain gauges stretch or compress, the current passing through changes as the torque creates pressure, adjusting the resistance.
As torque applies to a shaft, it introduces a twisting force, and this twist causes the strain gauges to stretch or deform. As the gauges deform and the current changes, the difference is recorded using a Wheatstone bridge, a type of circuit that compares a constant flow of electricity against an unknown current.
This difference in current is what a torque sensor uses to measure the amount of torque a shaft is experiencing. That reading is sent electronically to the output panel, which converts the readings into usable information, which you can use to adjust power, speed, and other factors to improve efficiency while preserving your equipment.
Types of Torque Sensors
In general, there are two types of torque sensors: static torque sensors and rotary torque sensors. While there are countless variations of models and applications for each of these types of torque sensors, it’s essential to understand the underlying properties of how each model works.
Here are some of the key differences between these two sensor types.
-
-
Static Torque Sensors
-
Also known as a reaction torque transducer, static torque sensors measure torque at the point where it meets the ground. These sensors usually involve two flanges, one attached to a sturdy, fixed element and the other with the rotating part. The gauge then measures the shearing force between the two flanges.
These sensors are usually less complex than rotary torque sensors, which gives them several advantages. Although they still rely on wires or cables to transmit signals, they tend to be less expensive, require less maintenance, and outlast the rotating elements they’re measuring.
However, static torque sensors also have limited uses, especially in the agricultural field. Instead, they are used primarily for testing and tool calibration, like calibrating torque wrenches.
While these sensors have some utility for agriculture, most farmers will use rotary torque sensors much more frequently.
-
-
Rotary Torque Sensors
-
Unlike a static sensor, rotary torque sensors must rotate with the shaft itself, operating in line with the rotation. Because of this, the sensor can’t have any attached wires, as they would quickly become bound up in the shaft and rendered useless.
Instead, rotary torque sensors transmit data wirelessly to a receiver, where it is interpreted and read.
A rotary torque sensor is typically attached to the shaft itself, located between the motor driving the rotation and the load connected at the other end. This attachment allows the sensor to measure the torque being applied along the shaft, helping to calculate both power and stress forces acting on the shaft.
Because the sensor is on the shaft, it has to transmit the forces to the sensor itself. The transmission can be achieved either through a keyed shaft (where the sensor is attached to the shaft with a piece of metal, or key, inserted into a slot cut into the shaft) or slip rings, which sit between two bearings in the sensor housing.
To get the most accurate torque measurements possible, it must account for any deflections across the shaft resulting from side loads, usually due to a heavy load at the far end of the shaft. Therefore, the only measurements a rotary torque sensor should be taking are those occurring in a clockwise or counterclockwise pattern around the shaft.
While these sensors are usually more expensive, they provide invaluable real-time data, especially in agriculture.
Let’s take a look at some of the many ways farmers can benefit from torque sensors.
How a Torque Sensor Helps the Agriculture Industry
When it comes to agricultural machinery, you’re probably looking for a few key characteristics. Everything on your farm needs to be durable to stand up to the long hours and hard work you need your equipment to perform. Your machinery needs to be efficient to get as much work done as quickly as you can.
Lastly, your farm equipment needs to be reliable. You need to trust that your machines are going to work every time you turn them on.
Torque sensors play a huge role in all three of these major needs, and companies like APG do everything they can to make sure you get your money’s worth from your sensors.
Agricultural torque sensors need to withstand the punishment of the daily work farmers need to accomplish, and part of that is ensuring that they provide you reliable, accurate information every time.
Consider a combine harvester, which requires several different torque sensors working together. Starting from the front end, the reel and the platform auger rely on torque to accomplish their work.
During harvests, any variations can lead to overdriving the torque, whether they stem from the uneven ground or particularly dense growth areas. A torque sensor can detect this imbalance, adjusting the drive to keep the combine working without damaging the machinery or the crops.
Next, the conveyors and the auger screws move the harvest through the combine. Both rely on torque sensors to keep material moving smoothly. Unfortunately, these areas are susceptible to jams. While the high torque power of the auger usually overcomes any obstacles, the sensor can detect when more power is needed, saving you time and fuel.
Finally, once your combine is full, the unloader mechanism relies on another auger to move harvested material up into the unloading pipe. An additional torque sensor regulates the speed and volume of grain passing through this pipe, ensuring you get all of the material out of your combine.
Of course, harvesting isn’t the only place where torque sensors are valuable. For example, fertilizer spreaders and similar tools are much more efficient when used in conjunction with torque sensors.
In fertilizer spreaders, for instance, a torque sensor can be used to adjust several aspects of fertilizer distribution. Constantly monitoring torque in your spreading equipment allows you to ensure that you’re spreading your fertilizer as evenly and efficiently as possible. In addition, sensors can detect differences in material, adjusting hydraulics, power, and other factors to ensure you aren’t wasting fertilizer or fuel.
There are many other instances in which you’ll come across torque sensors, from poultry feeding machines to other applications. These functions use paddle wheel switches, which distribute small particles from bins and hoppers using specific torque settings, which allows you to adjust the distribution width of the bits.
Another practical application is monitoring the motors that power your farm equipment. Keeping everything running can be difficult between the challenging environmental factors and the heavy wear and tear these machines endure throughout the year. With effective torque sensors, you can continually monitor your engine performance.
Not only can you prevent breakdowns by tackling minor problems before they get bigger, but you can also reduce excess wear by integrating these sensors into the operation of your equipment. In addition, these sensors allow you to keep your equipment running at peak efficiency, driving your machine hard without running the risk of overdoing it.
Finding the Right Torque Sensors for You
As you can see, torque sensors offer several advantages to those working in agriculture. From increasing efficiency to reducing the number of hours (and potentially crops) lost from breakdowns and other delays, top-notch torque sensors can quickly pay for themselves.
If you’re interested in learning more about how you can get the most out of your torque sensors, contact the team at APG. We’ll use our expertise to give you all of the information you need about sensor technology and help you get started on adding the latest, most sophisticated sensors to your equipment.
WRITTEN BY
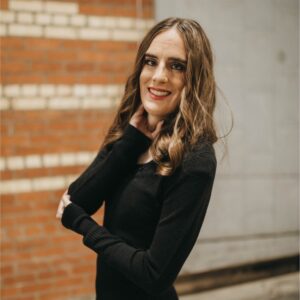
Sami T.
Sami Thompson is APG’s Marketing Technical Writer and has been with the company since 2022. With a master’s degree in English from Utah State University and a 40-page thesis publication under her belt, Sami has a demonstrated strong writing background. In her free time, Sami enjoys reading and birdwatching.