Proper load resistance is important in DC control and communication circuits. Control networks need it to function, and it determines how power is flows within a circuit. Here at Automation Products Group, Inc. (APG), we’ll define load resistance, what it’s for, and how a control network fits into it.
Load Resistance Defined
At the most basic level, load resistance is the cumulative resistance of a circuit, as seen by the voltage, current, or power source driving that circuit. This includes the resistance of the wires and the resistance of any devices connected to those wires. Everything between where the current goes out and where the current comes in contributes to load resistance.
What Is a Load Resistor?
A load resistor is a component that has the sole function of increasing the load resistance of a circuit to a specific level. It’s an output testing device used as an ideal output while designing or testing an electrical circuit.
Load resistors are used for impedance matching, maximum power transfer, and to improve output stability as well as to ensure a minimum of current flow. Load resistors are used at the output of a circuit to increase or decrease the power to the load.
What Is Load Resistance Used For?
The load resistance can serve as a variable to check the performance of the power source depending on the different load conditions.
Now, let’s look at two ways load resistance can be critical to proper operation of a DC control or communication circuit: line separation and signal conversion.
Line Separation
Modbus control networks, and others similar to Modbus, use two wires for communication. The voltage relationship between the two lines (A higher than B, or B higher than A) is an integral part of how the communication between devices works. For effective communication between server and client units, the voltage between the two lines must be consistent across the entire network.
Modbus networks use load resistors at each end of the network to accomplish this voltage stabilization. Since these resistors are placed at the ends, we call them terminating resistors instead of load resistors. However, if the server device of a given network is at one end, rather than at an intermediate point, the internal resistance of that server device behaves as the terminating resistance. So the terminating resistor at the opposite end of the network will need to be matched to the internal resistance of the server device.
Another way to look at this is through the following example. Two parallel wires have a resistor connected between them at each end. If DC voltage is applied at one end and the resistors are matched, the voltage at the other end will be the same. But if the resistors are not matched, especially if they are significantly different in size, the voltage at the far end will be different. This causes a mismatched current to flow in the circuit and disrupt the communication.
Thus, matching the load resistance to the source resistance is extremely important for this type of network.
Signal Conversion
Other communication and control networks, such as HART, use load resistors to convert current signals to voltage signals.
For instance, a HART transmitter that sends a 4-20 mA signal can’t communicate directly with a HART analog input card that detects 0-5 VDC signals. However, running the 4-20 mA signal through a 250 Ω resistor will create a 0-5 VDC signal that the input card can understand. In this instance, rather than using the load resistor to maintain voltage, we’re using it to create a voltage.
Check Your Documentation
These are just two ways that control networks are dependent on specific load resistors. If you’re having trouble with your control network communications, be sure to check the documentation for your devices to see if load resistance could be part of the problem.
We come across this issue more often than you might think. It can be a difficult detail to identify, causing downtime and frustration. This is one of several examples of wiring and networking issues that can alter or altogether ruin an otherwise good reading from a healthy sensor.
Contact us if you have questions regarding the wiring of your APG devices. Our Applications Engineers are happy to help you.
WRITTEN BY
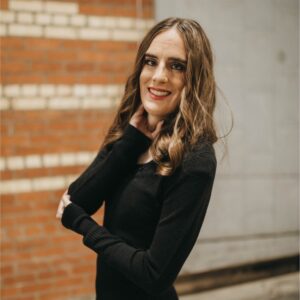
Sami T.
Sami Thompson is APG’s Marketing Technical Writer and has been with the company since 2022. With a master’s degree in English from Utah State University and a 40-page thesis publication under her belt, Sami has a demonstrated strong writing background. In her free time, Sami enjoys reading and birdwatching.