A level transmitter is used to measure the level of a liquid in an open or closed tank. It works by sending out a signal proportional to the fluid level and then measuring this signal with its sensing element. At Automation Products Group, Inc. (APG), we offer several types of level transmitters, such as submersibles, pressure transducers, hammer unions, and digital pressure gauges.
How to Calibrate a Level Transmitter
A level transmitter needs to be calibrated before it can be used. This process involves setting the device’s output signal so that it accurately reads the actual fluid level. The calibration procedure will vary depending on the type of level transmitter being used.
Submersibles should be sitting at least 6 inches below the surface of the liquid they’re measuring. The output signal should be adjusted so that it reflects the actual fluid level. Pressure transducers, on the other hand, should have their sensitivity adjusted so that it’s consistent with the desired range of measurement. Hammer unions require adjustments for inline pressure to ensure proper readings. Lastly, digital pressure gauges must be calibrated using a calibration device.
With proper calibration, a level transmitter can provide accurate information about fluid levels in open or closed tanks. This data can be used to make sure that processes are working properly and that materials are safely handled. By understanding how a level transmitter works and the necessary steps for calibrating it, companies can ensure that their operations run smoothly.
Submersibles (PT-500 Series)
Submersible transmitters, such as the PT-500 Series, are designed to be installed in the tank itself and measure fluid level using a pressure transducer. The pressure transducer converts liquid pressure into an electrical signal that can be read by the transmitter’s electronic circuitry. A submersible transmitter is generally easy to install and calibrate.
Pressure Transducers (PT Series)
Pressure transducers, like the PT Series, are used to measure pressure in liquid tanks. The pressure is measured with a sensing element that typically consists of a diaphragm and strain gauge. This type of transmitter can be used to measure differential or absolute pressure. When calibrated correctly, it can produce accurate readings over a wide range of pressures.
Hammer Unions
Hammer unions, mostly used in the oil & gas industry, are specialized pressure transducers that measure pressure differences between two points in a system. The sensing element consists of two diaphragms linked together by a mechanical linkage system. When pressure is applied to one side of the diaphragm, it moves the other side and creates an electrical signal that can be read by the transmitter’s electronic circuitry.
Digital Pressure Gauges (PG Series)
Digital pressure gauges, like the PG series, measure absolute or gauge pressure in liquid tanks using a sensing element similar to those used in pressure transducers. The difference is that digital pressure gauges have a built-in digital display that can be programmed to show different units of measurement, such as psi, bar, or inHg. Digital pressure gauges are easy to install and calibrate and require minimal maintenance.
No matter which type of level transmitter you choose, it’s important to ensure the device is properly installed and calibrated for accurate readings. Regular maintenance should be carried out to ensure that the device is working properly and that the readings are accurate.
At Automation Products Group, we offer a wide range of level transmitters to meet your needs. Our experts can help you find the right device for your application and provide support with installation and calibration. Whether it’s a submersible, pressure transducer, hammer union or digital pressure gauge, our team is here to help you get the most out of your level transmitter. Contact us today to learn more about how our products can help you measure levels in your tank with accuracy and ease.
WRITTEN BY
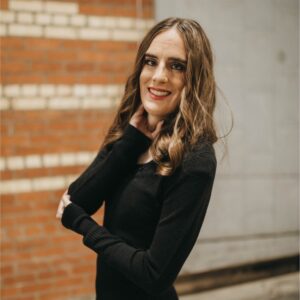
Sami T.
Sami Thompson is APG’s Marketing Technical Writer and has been with the company since 2022. With a master’s degree in English from Utah State University and a 40-page thesis publication under her belt, Sami has a demonstrated strong writing background. In her free time, Sami enjoys reading and birdwatching.