Two of the most well known protection methods for instrumentation in hazardous areas are Intrinsic Safety and Explosion Proof. The difference between the two is quite large, and amounts to the idea of prevention vs containment. Then there are the practical differences, which are largely based on how the two are wired.
We’ll discuss these basic differences and the merits of each.
Prevention vs Containment
There are really three basic methods to stop the ignition of fires and explosions in hazardous areas. They are:
-
- Containment
- Segregation
- and Prevention
The containment school of thought allows the ignition to happen, but keeps it from spreading to the open atmosphere where it becomes dangerous. The only method of containment is to use explosion proof devices.
Segregation separates ignition sources and hazardous substances using pressure, oil, powder, or resin.
Finally, prevention controls the source of ignition, never allowing enough energy to make ignition possible. By far, the most representative method of prevention is using intrinsically safe devices.
Segregation is uncommon for electrical instrumentation, and is therefore outside the scope of this article. We’ll focus instead on explosion proof and intrinsic safety.
Containment via Explosion Proof Devices
How It Works
An explosion proof device has a housing that’s able to contain an ignition, keeping the explosion from spreading to the open atmosphere. This is accomplished through the use of heavy duty enclosures and conduit.
Examples we have of explosion proof devices in our sensor line up include the MPX and RPM continuous float level sensors. These sensors have a housing that’s undergone rigorous testing to ensure that the enclosure can contain an explosion.
But the sensor housing plays only a minor role in the overall installation. Any wires that are connected to the sensor must also be enclosed, so wires are run through explosion proof conduit pipes and hoses. This is where the majority of the work and cost for explosion proof installation comes into play.
The Pros and Cons
The explosion proof method can be employed for any type of electrical instrument and is not limited to just low powered units.
Wiring an explosion proof device is well understood, and while a bit expensive, it’s perceived to be straightforward. Many older operators that we work with prefer explosion proof wiring because it’s been around for a long time and is familiar.
However, explosion proof wiring is expensive due to the conduit, enclosures, and seals. In addition, the device housing and the wiring require vigilant maintenance checks for damage and leaks. Most experts agree that this method involves more safety risks than others since an explosion is still allowed to happen. If damaged and leaking, disaster will follow.
Prevention via Intrinsic Safety
How It Works
Intrinsically safe devices never allow an ignition to happen in the first place. The devices use very low power currents, so low that fires and explosions are simply impossible – even in fault conditions, like a broken wire or circuit board damage.
Explosions require the presence of three factors: fuel, oxygen, and a heat (ignition) source. While the explosion proof method limits the supply of fuel and oxygen by containing an explosion, intrinsic safety takes explosions out of the equation.
Just like the explosion proof method, there’s more to intrinsic safety than the instruments used. The wiring is very important to ensure the installation meets code. However, the process is much less involved.
In this case, the wiring requires the addition of an intrinsically safe barrier or isolator (one or the other). These devices limit the power that flows through the hazardous area, ensuring that a power surge can never overwhelm the circuit and cause an explosion.
Any wires that are run through the hazardous area to the devices must first run through a barrier or isolator. But conduit and seals are not required.
The Pros and Cons
Intrinsically safe is considered the superior method for hazardous locations since it altogether prevents an explosion from taking place. For this reason, we recommend using this method whenever possible.
We often hear concerns over the expertise required for intrinsically safe wiring installations. While intrinsic safety does require an extra step, it’s not as complicated as you may think. Furthermore, it doesn’t require a stringent maintenance policy that requires operators to evacuate rooms for testing and programming of instrumentation.
The major downside to intrinsic safety is that it can’t be used for all applications. It’s simply impossible to run certain types of devices, such as lighting fixtures and motors, on such low currents and voltage.
What are your opinions about the merits of Explosion Proof and Intrinsic Safety? Do you prefer conduit or barriers? Contact us at sales@apgsensors.com and we’ll discuss your methods and answer any questions you may have.
WRITTEN BY
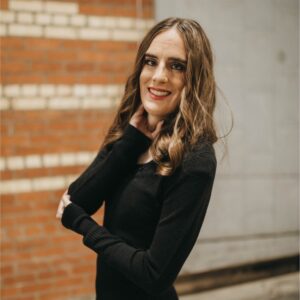
Sami T.
Sami Thompson is APG’s Marketing Technical Writer and has been with the company since 2022. With a master’s degree in English from Utah State University and a 40-page thesis publication under her belt, Sami has a demonstrated strong writing background. In her free time, Sami enjoys reading and birdwatching.