Basics of Tank Level Indication
To know how to measure oil in industrial tanks best, we need to go over how to achieve tank level indication. The measurement of the position of an interface between two media is known as level measurement. These media are usually a liquid and a gas, but they could even be two liquids.
A comprehensive kind of physical principle applied to measurements of liquids, solids, and slurries levels such as pressure, level-sight, radiation, sonic principles, electrical properties, etc. Different regulations govern the operation of level devices. The three major categories include:
-
- measuring the position (height) of the surface
- the head pressure
- the weight of the material through load cells
Based on the above categories, various technologies are available to measure liquid levels. They include:
-
- Visual
- Hydraulic head
- Displacer
- Capacitance
- Conductance
- Sonic and ultrasonic
- Weight
- Load cells
- Radar
- Fiber optics
- Magnetostrictive
- Nuclear
Relying on the type of level measurement chosen, consider many parameters when using level-measuring devices. Ignoring such parameters may result in an outsized margin of error or measurement with a short lifetime. In addition, level-measuring devices, like all other pieces of instrumentation and control, should be installed in a location that allows for simple inspection and maintenance.
Answer the following questions to determine which type of level sensor to use for an application:
-
- What is the material to measure: liquid or solid?
- Can the sensor be placed within the chamber, or should it be external?
- Would you like contact or non-contact level measurement?
- What’s the acceptable degree of accuracy?
- What are the application’s temperature and pressure ranges?
- Is the density of the liquid changing with time?
- Is point level or continuous measurement required?
- What level measurement range do I require?
- Is the measured material electrically conductive?
- Will the material coat or build around surfaces?
- Does foam, vapor, or turbulence occur at the surface of the liquid?
- What about output? Do I need: analog, relay, digital display, etc.?
Construction materials of the sensor are essential and can not affect the material within the tank. A tank level detector can be customized for a selected application. In that case, the user should research what method to use in their industry before purchasing the instrument.
Floating System As A Level Indicator
In this system, a float movement depends on the liquid surface. The results of this vertical movement of the float are shown to the observer. Actuating a float switch alongside or creating a quantitative analog signal in its route supported the variation of the resistance placed inside the stem of the instrument because the magnetic float moves.
Magnetic floats shouldn’t be used for liquids containing iron particles or other strongly magnetic materials. Magnetic Float Type Level Switches could also be available both as horizontal and vertical versions. The horizontal type is used on the sidewall of tanks. Its operating principle is that the rising liquid level tilts the float upward, the magnet attached to the highest of the body actuates the switch.
The vertical type is installed on the very best of the tank. Thus, the floats are made from stainless steel or other materials like plastic, Teflon, etc., suitable for liquids with a density above the precise gravity of the float.
If the instrument should be connected to the side of the tank, a selection of chambers could even be used for side connection. Moreover, the device can have multiple floats and switches to manage and notify the operator of the numerous liquid levels within the tank.
When using magnetic floats in level indication, they use the magnetostrictive principle to provide continuous level data without direct contact between the indicator and thus the fluid within the system. The float inside the hermetically sealed tube moves with the changing liquid level, and since it travels, the colored wafers (flag display). Sincere magnetically coupled to the float, rotate, and color changes. The wafers should be visible within the dark without light. A ruler is mounted along the wafer column to the distance unit or a percentage of the total height.
A transmitter or magnetic switches are often installed along the tube on these floating systems to act as an indicating level.
The Magnetic Level Gauge (by-pass) is an improved alternative to sight gauges (glass tubes) to visually monitor liquid levels in boilers, storage tanks, etc. Replacing the sight gauges with magnetic level gauges results in improved safety, increased visibility (10 times), reduced maintenance, and lower overall operating cost throughout the life cycle.
Dial Liquid Level indicators are for level measurement of bunker-c, water, diesel fuel, etc. Easy installation of these transmitters makes them the right choice for several level measurement and control applications. The operating principle is premised on the buoyancy of float and spring force. As the float rises and falls, the spring displays the extent on the front scale and produces an analog signal. This system is also available with switching contacts or analog (4…20 mA) output.
Pressure Type Measurements
The pressure at a given depth for a static liquid is the load of the liquid working on a unit area at that depth plus any force acting on the surface of the liquid. Thus, level measurement predicated the pressure measurement is also called hydrostatic tank gauging.
To determine the hydrostatic pressure of a column of liquid, multiply the density of the liquid by the height of the liquid column. Therefore, if we all know the hydrostatic pressure measured by the pressure sensor and the density of the fluid therein specific temperature, we will calculate the height of the liquid column.
Use pressure measuring elements to infer that the liquid level has been achieved successfully in both open tanks (the top of the liquid column is open to the atmosphere) and closed tanks (liquid is in a pressurized tank).
When measuring a level in an open tank, the effect of atmospheric pressure is compensated by utilizing a gauge pressure device. Thus, the pressure reading is directly proportional to its specific gravity and the height of the liquid. While in closed tanks, the effect of the pressurized air above the liquid column must inherit consideration and be deducted from the measured value of the pressure at the bottom of the fluid column. Therefore, differential pressure cells (DP cells) are mandatory for closed tanks by measuring two forces.
Capillary tubes of the diaphragm seals must be as short as possible and shielded from the radiation heat and ambient temperature.
Radar Level Measurement
Radar level measurement is based on the principle of measuring the time required for the microwave pulse and its reflected echo to form an entire return trip between the non-contacting transducer and thus the sensed material level. Then, the transceiver converts this signal electronically into level/distance and depicts it as an analog and/or digital signal. The transducer’s output often selected by the user is directly or inversely proportional to the span.
Pulse radar takes many ‘shots’ every second. The return echoes from the merchandise surface are sampled and averaged, which is especially important in challenging applications where small amounts of energy are being received from low dielectric and agitated product surfaces. The averaging of the center beat technique reduces the noise curve to permit smaller echoes to be detected.
The achievable accuracy of a current radar level meter depends heavily on the following:
- antenna design
- mechanical installation
- state and quality of the electronics
- echo processing software employed
The accuracy of an existing instrument is additionally dependent upon signal-to-noise ratio and interference.
Level Measurement With Radar Instrument For Agitated Liquid
High-frequency radar transmitters are prone to signal to scatter from agitated surfaces. The high-frequency radar will receive considerably less signal than an equivalent 5.8 GHz radar when agitated liquid surface. Installing the radar using a stilling well/ bypass tube ensures a calm surface with no scattering of the echo signal.
Condensation And Build-Up Effects On Radar Instruments
High-frequency radar level transmitters are more inclined to condensation and product build-up on the antenna. However, a 6″ horn antenna with a 5.8 or 6.3 GHz frequency is unaffected by condensation and build-up.
Ultrasonic Level instruments
Ultrasonic level instruments operate on the basic principle of using sound waves to determine liquid/solid/slurries. In addition to standard level or volume measurement, they can monitor open channel flow, determine the actual volumetric throughput in lift stations, measure differential level and control the pumps.
Ultrasonic Level Transmitters consist of two elements, a high-efficiency transducer and) an associated electronic transceiver. Together, they operate to determine the time for a transmitted ultrasonic pulse and its reflected echo to make a complete return trip between the non-contacting transducer and the sensed liquid level. A piezoelectric crystal inside a top-of-tank mounted transducer converts electrical pulses into sound energy that travels in the form of a wave at the established frequency and at a constant speed downward onto the surface of the material whose level is to be measured. Echoes of these waves return to the transducer, which performs calculations to convert wave travel distance into a measure of level in the tank. The time-lapse between firing the sound burst and receiving the return echo is directly proportional to the distance between the transducer and the material in the vessel. The medium is usually air over the material’s surface, but it could be a blanket of other gases or vapors. The instrument measures the time for the bursts to travel down to the reflecting surface and return. This time will be proportional to the distance from the transducer to the surface and can determine the level of fluid in the tank. This fundamental principle lies at the heart of the ultrasonic measurement technology and is illustrated in the equation:
Distance = (Velocity of Sound x Time)/2.
These non-contact devices are available in models that convert readings into 4–20 mA outputs to DCSs, PLCs, or other remote controls.
The frequency range for ultrasonic methods is in the range of 15…200 kHz.Several factors must be considered for practical applications of ultrasonic measurement. A few key points are:
- The speed of sound through the medium (usually air) varies with the medium’s temperature.
- Therefore, suppose the temperature of the sound medium is to remain constant instead of using either the integral temperature compensation or the remote sensor. In that case, the desired temperature may be entered during the transceiver configuration.
- The presence of dust/heavy foam on the material’s surface can act as a sound absorbent. Therefore, a beam guide is attached to the transducer to enhance performance where foam/dust or other factors affect the wave travel to and from the liquid surface.
- Use of a damping adjustment in the instrument or a response delay may help overcome the extreme turbulence of the liquid that can cause fluctuating readings. Damping slows down the display rate, especially when liquid surfaces agitation of material that falls into the sound path during filling.
Capacitance Level Instruments
Capacitance level instruments operate on the basic principle of the variation of the electrical capacity of a capacitor formed by the sensor, the vessel wall, and the dielectric material. A capacitor is made of two conductive plates which are isolated from each other by a dielectric.
The storage capability of a capacitor is directly dependent on the plate’s areas (A), their distance (d), and the dielectric constant of the material between the plates (ε).
C = kεA/d
Where C is the value of capacitance, expressed in Farad.
k is a constant with a value of 0.225 or 0.0885 depending on the units used.
The dielectric constant of the process material is the most critical consideration of this level measurement application. The higher the dielectric of the process material, the easier and more reliable would be the level measurement. Temperature, moisture content, humidity, and density can change the dielectric constant of the process materials must be taken into account.
Moreover, it is essential that the probe’s tip instead of the entire probe be covered with the process material—typical insertion probe lengths ranging from 20 to 40 cm.
Wet and sticky materials cause permanent coating and build-up to the probe and introduce errors in the level measurements. Therefore, it is recommended to use a Teflon insulator on the conductive probe when the dielectric constant of the process material is high.
Installation of the probe must be such that it does not contact the vessel wall or any structural element of the vessel.
This type of level sensor is suitable for interface measurement.
Conductivity Level Measurement
Conductivity level measurement is similar to the capacitance technique. However, conductivity level sensors detect the medium’s resistance while the process material covers its electrodes.
This method is usually used for water vessels and in processes like water & wastewater treatments, chemical, pulp & paper, food, wine, biological, etc. They’re mounted multi-point sensors with up to four probes or three probes and one reference electrode.
They can be mounted on various open or closed vessels (suitable for pressurized tanks) or ordered because of the submersible version for level detection in wells or deep tanks. They’re going to control the differential of minimum and the maximum level, with an adjustment for sensitivity.
Vibrating Fork Level Measurement
Vibration Fork Level Switches are designed considering vibration at its frequency by a pair of piezo-ceramic discs. The frequency and amplitude of vibration change when coming into contact with the medium. This change is detected, processed, and converted into a switch signal.
They can be used for liquids with a density of more than 0.7 and on free-flowing granules and powders of light and medium density. In addition, they cover an outsized variety of applications such as overfill or rehearsal protection, pump controls, high/low fail-safe limit switch, dry/wet indication in pipes.
High excitation frequency in a sound vibration sensor ensures interference-free operation and enables high vibrating fewer and turbulent liquid surfaces. This measurement technique is exceptionally well suitable for top viscosity liquids (response time will be longer). Thus, the operation won’t be affected by the foam and gas content of the material. Vibration forks are often utilized in liquid, solid, and slurry level detection.
Thermal Dispersion Level Measurement
The principle of thermal level sensors is to differentiate between the temperatures of the vapor above the liquid. The fluid itself or, more commonly, the rise in thermal conductivity as an inquiry becomes submerged within the tactic liquid. One of the only thermal level switch designs consists of a temperature sensor heated with an unbroken warmth input. While the probe is within the vapor space, the temperature remains the same. This is because the low-conductivity vapors don’t carry much heat far away from the probe. When the probe is submerged, the liquid absorbs more heat dropping the probe temperature. The switch is actuated when this alteration in temperature occurs.
Thermal level switches are set to detect the presence or absence of any fluid as all process materials have a characteristic heat transfer coefficient. Therefore, these switches are often utilized under challenging services, like interfaces, sludge, and slurry applications. They might detect thermally conductive foams if spray-cleaned after each operation.
Thermal level and interface switches haven’t any mechanical moving parts and are rated for top pressure. Therefore, they work best with non-coating liquids and a slurry with 0.4-1.2 density and low to medium viscosity.
Optical Level Measurement
In level measurements, the optical sensors depend on the sunshine transmitting, reflecting, or refracting properties of the method material. A refracting sensor relies on the principle that light or infrared changes direction (refracts) during passing through the interface between two media.
When the sensor is within the vapor phase, most of the sunshine from the LED reflects within a prism. When the prism is submerged, most of the sunshine refracts into the liquid, and therefore the amount of reflected light that reaches the receiver drops substantially. Thus, a drop by the reflected light signal indicates contact with the method liquid.
One sort of transmission sensor relies on the refraction principle utilizing an unclad, U-shaped fiber optic cable. A light source transmits a pulsed beam through the fiber cable, and therefore the sensor measures the quantity of sunshine that returns. The utilization of fiber-optics makes the system impervious to electrical interference, and a few designs also are intrinsically safe., A level switch that combines an optical with a conductivity-type level sensor to determine the presence of both water (conductive) and hydrocarbons (non-conductive).
Finding The Right Tank Level Indication Tool
There are many options for measuring your various liquids including oil. Knowing which one to choose is no small feat, but the experts at APG sensors are here to help you along your way.
Feel free to give us a call and we can find the right one for you.
WRITTEN BY
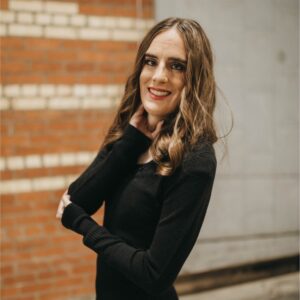
Sami T.
Sami Thompson is APG’s Marketing Technical Writer and has been with the company since 2022. With a master’s degree in English from Utah State University and a 40-page thesis publication under her belt, Sami has a demonstrated strong writing background. In her free time, Sami enjoys reading and birdwatching.