Calculating the width of an ultrasonic beam can be a little tricky. Luckily, the experts at Automation Products Group, Inc. (APG) have done it enough times that we can give you a solid reference point. We have to make a key assumption in order to do it: maximum sensitivity settings.
If your ultrasonic sensor’s sensitivity is turned up all the way, then the beam expands 9° off center for about 12 to 15 feet, after which it narrows again. So for the first 12 to 15 feet, we can determine your beam width, or spread, with reliability.
How do I calculate the beam spread?
The typical ultrasonic sensor beam spread at maximum sensitivity is 38 inches across at 10 feet away from the sensor’s face.
To calculate the beam spread at maximum sensitivity, use the following formulas:
Distance in Feet X 3.8 (constant) = Beam Spread (inches)
Example: 10 feet X 3.8 = 38 inches
Distance in Inches X .317 (constant) = Beam Spread (inches)
Example: 120 inches X .317 = 38 inches
Maximum sensor sensitivity usually isn’t needed to obtain the best reading. However, the fastest method to get things working right in the field is to adjust your sensor settings until an optimal reading is achieved.
APG ultrasonic sensors have an Auto Sense mode, which optimizes readings automatically in most applications. If manual adjustment is needed, contact us and we’ll guide you through it.
Why does it matter?
Beam spread becomes important when trying to send the signal between physical obstructions. Many tanks and wells have pipes, ladders, or other equipment attached to the walls. If an ultrasonic beam hits the obstacle, it returns a signal back to the sensor and give a false reading.
Why does the beam retract after 12 to 15 feet?
Like the ripples in water, sound waves only carry so much energy, which is focused in the center. Depending on your model, the outer reaches of the sound wave become too weak to return to the sensor after 12 to 15 feet. While there’s still a sound wave traveling at 9° from its origin, it will never make it back to the sensor. This effectively narrows the beam spread once the apex is reached. Again, the specifics all depend on the model and the settings of your ultrasonic sensor.
For more help with adjusting your ultrasonic level sensor, feel free to reach out to APG today. Our experts are ready to help you!
WRITTEN BY
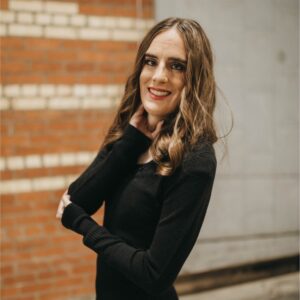
Sami T.
Sami Thompson is APG’s Marketing Technical Writer and has been with the company since 2022. With a master’s degree in English from Utah State University and a 40-page thesis publication under her belt, Sami has a demonstrated strong writing background. In her free time, Sami enjoys reading and birdwatching.