Float level transmitters rely on matching the right float with the right specific gravity, or density, of your liquid. While there are other specifications that matter (i.e. chemical compatibility, temperature, and pressure), the accuracy of your float level transmitter is tied directly to specific gravity.
Each float has a reference point where the float is calibrated. This is essentially the point on the float where the measurement is taken. Getting the liquid level to line up with that point is ideal. If we can’t, we just do an offset.
A simple calculation will tell you how closely your liquid level will line up with the reference point on your float. Here are the steps you need to take to figure it out.
Specific Gravity Levels Helping With Float
First, specific gravity (SG) of the float is important when purchasing a level probe. Make sure that it’s less than that of the liquid. If it’s greater than or equal to, you’ll have a sink, not a float.
For example, a float with the same SG of the liquid may or may not sink to the bottom, and it may or may not float to the top. It will likely sit somewhere in between.
If the SG of the float is only slightly higher than the liquid then it will sink to the bottom, though it may happen slowly. If the SG is a lot higher, it will drop like a rock.
Remember to pay close attention to the temperature range of the liquid media, as the SG will change with temperature. Make sure the float will always have a lower SG than the liquid at all expected temperatures.
Minimum Specific Gravity Difference Between Two Liquids
If you’re trying to measure the interface between two liquids, first you must determine if the liquids will separate when settled. The liquids separate by either differing molecular properties such as a polar solvent and a nonpolar compound being immiscible, or because they simply have a differing specific gravity.
It’s important to keep in mind that if there’s a separation between the two liquids, it doesn’t guarantee the ability to measure the interface. Float sensors depend on the specific gravity between two liquids and will not distinguish between different molecular properties.
Specific Gravity Of Liquids & Liquid Interface
For liquids, water is the reference with a specific gravity of 1. Less dense liquids such as ethanol and propane have specific gravity measures of .787 and .500 respectively, while more dense liquids such as mercury have a specific gravity of 13.663.
A common application for interface level measurement involves oil and water. Since oil is less dense with a specific gravity of .7, it will float on top of the water which has a specific gravity of 1. An effective level measurement will include two floats with different specific gravities. The first float must sit on top of the oil, so it will need to have a specific gravity of less than .7.
The second float must be dense enough to sink below the oil and sit on top of the water. Here at APG, we use a float with a specific gravity of .92 in order to achieve this.
The specific gravity between the two liquids must be different enough to allow a single float to sink below the less dense liquid (oil) and rest on the denser (water). Determining the minimum specific gravity gap required between two liquids is difficult since a number of factors are at play. However, we suggest a difference of at least .05 between the two liquids.
Float Level Gauge Submersion Levels
Once you know the float will float, now it’s time to find out what percentage of the float will be under the surface. This will tell you exactly where the surface of the liquid will be on the float. The calculation is simple. Simply take the SG of the float and divide it by the SG of the liquid.
So a float with a .65 SG in water (SG=1) will be submerged 65%, whereas in methanol (SG=.786) it would be submerged 82.7%.
That’s .65/1 for water or .65/.786 for methanol.
Keep in mind that water is the typical reference liquid for density, with a specific gravity of 1. Less dense liquids will have a lower specific gravity, such as propane at 0.5. Higher density materials have a higher specific gravity. For example, Mercury at room temperature has a specific gravity of 13.63.
Calibration for Float Transmitters
With that bit of information handy, you now know how far up the float the liquid surface will be. Now you need to determine how far it is from the reference point (sometimes called the calibration point). Use that distance to program an offset and you’ll end up with an accurate reading.
The offset can be programmed into some sensors. If yours can’t do it, then have your control technician program it into your PLC or controller.
Another option would be to compare your float level transmitter reading to a physical measurement and trim the sensor’s output to match.
Mind The Temperature Affect
Finally, beware of temperature changes. They change the SG of your liquid and is the main variable of concern. Find a table of your liquid’s SG over a spectrum of different temperatures. Now find out what temperature range your liquid will experience in its tank or container.
Cross-reference the data in the table to your temperature range to find the SG swing that you’ll be dealing with. Next, attempt to establish an average or a normal and calibrate your offset to match. This will give you the best results.
While SG changes with temperature variation is minimal, and typically within or near the sensor’s error band, compensating during the commissioning of the sensor will give you better results.
If you really want to optimize your accuracy, you could create a table of SGs at certain temperatures, install a temperature sensor if needed (our magnetostrictive probes have temperature options), and use your control system to automatically compensate for you. It’s work, but it’s very doable if you can gather all the right information.
These four steps will give you the best accuracy from your float level transmitter.
At APG, we design our floats to show the level where the center of the float rests. If the float is too high or too low in the liquid, this will introduce inaccuracy into the application.
We customize our level floats to match the specific gravity of your liquid, to optimize accuracy. However, not everyone tells us the specific gravity of their liquid. Make sure you let us know what it is, so we can manufacture your float accordingly.
If you have any questions, please contact us or send us an email. We’re experts on these sensors and can help you improve your performance and reliability.
WRITTEN BY
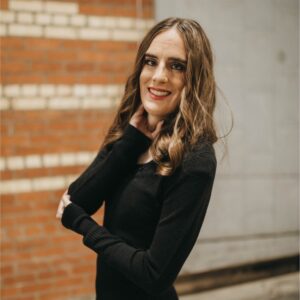
Sami T.
Sami Thompson is APG’s Marketing Technical Writer and has been with the company since 2022. With a master’s degree in English from Utah State University and a 40-page thesis publication under her belt, Sami has a demonstrated strong writing background. In her free time, Sami enjoys reading and birdwatching.