With wiring and connections, several problems can prevent a sensor from reading properly. At Automation Products Group, Inc. (APG), we’ve seen many issues with wiring. This is why we’ve put together this guide on the five most commonly identified wiring problems and their solutions.
Problem 1: Vibration and Loose Wiring
Vibration is common throughout industry. This can loosen terminated wires and break connections. Securing a sensor to power through the vibration is key, and we have several solutions available.
For battery-powered gauges, a battery strap keeps the batteries in place in severe vibration cases. Similarly, screw-down and spring-clamp terminal blocks prevent vibration from shaking wires loose in control instrumentation and panel boxes. Because we have customers using our sensors in high-vibration applications, APG routinely ties all internal wires down. We even fill the inside of our sensors with industrial potting to seal everything in place.
Problem 2: Electrical Interference
Electromagnetic interference (EMI) is a constant problem that technicians and engineers battle regularly. It’s caused by electromagnetic fields produced by power sources and high-power electrical equipment. Electrical motors, variable frequency drives, and power sources are a common source of noise.
The solution requires you to route signal cables away from sources of EMI and use shielded cable for your signals. If needed, you can route your cables in metal conduit. The key is to make sure your cable and conduit are properly grounded. As a rule of thumb, limit your shield grounding points to one. If you have two or more grounding points, make sure the electrical potential of each is the same. If you don’t, you may end up with ground loops that will only enhance the EMI.
Problem 3: Corrosion and Moisture
Exposed connections are vulnerable to nearby corrosive elements, especially when moisture is present. Depending on the application, your wiring could experience airborne chemicals, cleaning agents, or salt spray, all of which will damage connectors and leads.
Using the right enclosures or properly rated equipment is crucial in any application where gases, moisture, or chemicals may be present. Sealed containers, appropriately IP- or NEMA-rated instruments, and the right materials to keep corrosion at bay.
Problem 4: Labeling and Identification
The lack of proper labeling can magnify a wiring problem. If you don’t know what the wire is connected to, you’ll waste a lot of time figuring it out. The problem is magnified when installation doesn’t follow the paper work. Cutting corners in your wiring will come back to bite you when the pressure’s on to get something fixed or replaced.
In extreme cases, software is used to sort out the details of each cable, such as where it’s connected, what signal it’s carrying (if any), etc. No matter what your method, make sure you follow the rules and stay disciplined.
Problem 5: Stress
Not all cables created equal. If your cable needs to withstand repetitive motion, weighted suspension, or even the occasional hit from a sledgehammer, you’ll need to take special precautions to protect the integrity of your wiring.
For example, wiring on a pick and place machine will need to handle repetitive motion. Stranded cable is best. We attach our PT-500 submersible pressure transducer to a cable with re-enforced strands to keep the cable from stretching if someone hangs the sensor by the cable. Our hammer union pressure transmitters feature a protective cage around the top of the sensor to prevent oilrig workers from smashing the cable and connector with their sledgehammers when tightening the wing nut.
Wiring doesn’t exist in a vacuum. It lives in harsh environments, and the right cable for the job must be chosen or breakage will occur.
Let us know if you have any questions related to wiring your level sensors or pressure transducers. Our application experts are ready to help!
WRITTEN BY
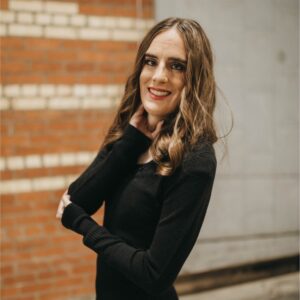
Sami T.
Sami Thompson is APG’s Marketing Technical Writer and has been with the company since 2022. With a master’s degree in English from Utah State University and a 40-page thesis publication under her belt, Sami has a demonstrated strong writing background. In her free time, Sami enjoys reading and birdwatching.