Old Reliable is reliable. And you trust your sensors to be reliable. Really, what’s the point of a sensor that’s not reliable? If you can’t trust the readings, what’s the point in having the readings? There isn’t one.
And yet, even precision Swiss watches need a tune up. So it’s safe to assume that your pressure sensor may eventually need to be recalibrated (we recommend about once a year). Can you do it? How do you it? Let’s take a look.
Potentiometer-Based Calibration
A potentiometer is a tiny, screw-in-and-out adjustment point, like the volume dial on a stereo.
Some pressure sensors have screws for Zero Adjustment, Span Adjustment, or both. Turning these screws will adjust the low-end output (Zero Adjust) or high-end output (Span Adjust). Generally, these screws will be located on the PCB, inside the body of the sensor. To adjust either output, you will need to:
- Open the sensor without disconnecting the output ports from the PCB.
- Accurately apply zero and full-scale pressure to the transducer. (We recommend at least ±0.1% of full-scale accuracy for the applied pressure.)
- Connect the sensor to an appropriate electrical source and monitoring equipment to verify sensor output.
- Start by adjusting the zero output, before adjusting the full-scale output.
A DC Power Supply, multimeter, and a pressure comparator are the only fancy tools you need.
Electromagnetic-Based Calibration
Electromagnetic-based calibrations come in two flavors: Magnet, and Shunt Calibration (often called Shunt Cal). Magnets are easy to use; Shunt Cal is tricky to understand, but simple to do. Let’s look at magnets first.
Rather than a potentiometer, some pressure sensors use magnets for their Zero Adjust. Usually a small magnet is held near the top or bottom of the sensor to increase or decrease (respectively) the zero output of the sensor. The full-scale output for these types of sensors is usually only adjustable by the factory. As with potentiometer-based calibration, you will need to:
- Accurately apply zero pressure to the transducer. (We recommend at least ±0.1% of full-scale accuracy for the applied pressure.)
- Connect the sensor to an appropriate electrical source and monitoring equipment to verify sensor output.
- To adjust the zero output lower, hold the magnet perpendicular to the lower end of the can.
- To adjust the zero output higher, hold the magnet perpendicular to the upper end of the can.
Side note: magnet adjustment of the zero output can be tricky if the zero output is 0 (e.g., 0 VDC, 0 mV, etc.). When the zero output is a non-zero value, as on a 1-5 VDC sensor, there are actual values less than the zero output (0.995 VDC, 0.85 VDC), so you can tell when you’ve adjusted the value too far and need to bring the output back up. When the zero output is 0, you don’t have that extra cushion below the zero output, and you can adjust the value so far that it can only be pulled back up by the factory.
Shunt Cal is different than the rest of the tools here, in that it calibrates not your sensor, but your control system. Shunt Cal works by electrically simulating a full-load across piezoresistive strain gauge-type pressure transducers, generating a full-scale electrical output. Thus, you can adjust your control system based on that full-scale output, allowing you to compensate for the load resistance of the cable between your transducer and controller. Especially for unamplified signals, the difference between 19.925 mA and 20.125 mA can be significant.
Software
The last technique we’re going to look at for calibrating your sensor is using software. For sensors connected to monitoring software, it should be easy to adjust the zero and full-scale outputs. For example, software controlling a 4-20 mA sensor might have a 4 mA calibration setting and a 20 mA calibration setting. In this way, software control does what both the Shunt Cal and previous calibrations techniques do: it adjusts the sensor’s output, and the control equipment’s reading of the output.
To calibrate your software-controlled sensor you will need to:
- Connect the sensor to the control software.
- Accurately apply zero and full-scale pressure to the transducer. (We recommend at least ±0.1% of full-scale accuracy for the applied pressure.)
- Using the software, adjust the zero and full-scale output calibration variables until the respective outputs of the sensor are correct.
As long as you have the appropriate tools, calibrating your pressure sensor shouldn’t be intimidating. If you’re feeling some trepidation, or just have some questions, please contact us via, phone, email, or on-line chat. And of course, you can always send your sensor back to the factory for recalibration.
WRITTEN BY
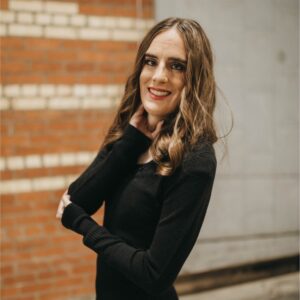
Sami T.
Sami Thompson is APG’s Marketing Technical Writer and has been with the company since 2022. With a master’s degree in English from Utah State University and a 40-page thesis publication under her belt, Sami has a demonstrated strong writing background. In her free time, Sami enjoys reading and birdwatching.